Thermal Spray Coatings
Thermal Spray Coatings
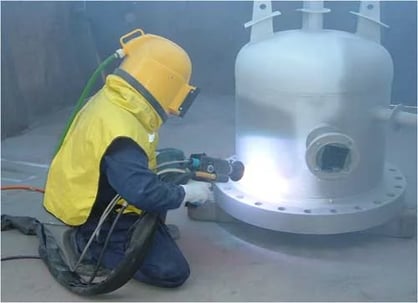

Norimax Thermal Spray Coating team comprises a very experienced group of engineers and technicians committed to providing the best quality application of thermal ARC-SPRAY and FLAME-SPRAY coatings for the oil & gas, power and marine industries in the SE Asian region.
Norimax management commitment to quality assurance is not matched by any other Thermal Spray specialist in this region. Our understanding of the extreme high standards and high quality assurance requirements for successful TSC applications is well recognized by the oil & gas operators in this region.
Norimax TSC management, TSC QA/QC team and TSC Sprayers commitment to high quality standards have been audited and approved by Shell Global Solutions International and is well recognized by other oil & gas operators.
TSC Standards and Qualifications
Thermal Spray Coating
Thermal Spray is a process whereby metals, alloys and non-metals are melted by a heat source and are released through spray guns by compressed air.
Norimax TSC team is committed to compliance with international standards such as ISO-14918 & ISO-14919, AWS C2.16, Norsok 501, etc.
Norimax TSC team is well-versed with company standards such as PETRONAS PTS 30.48.40.31, SHELL DEP 30.48.40.31 , EXXONMOBIL MPDS 29-02-07, etc.
Thermal Spray Coating
Thermal Arc Spray
Thermal Flame Spray
Thermal Flame Spray
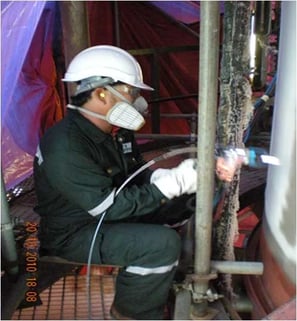
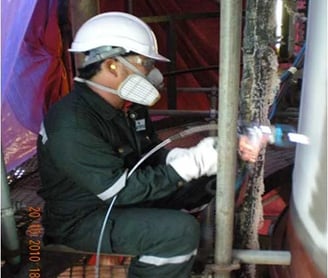
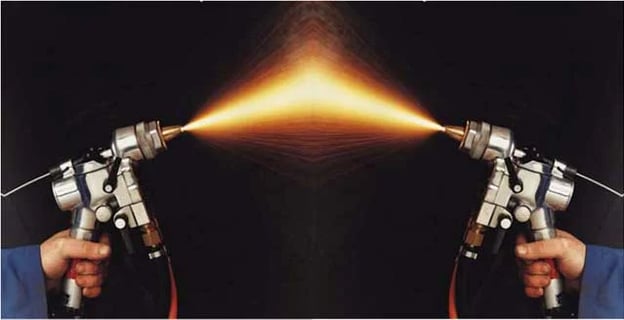
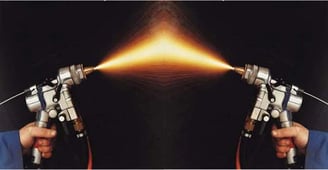
Flame Spray Equipment Set-up
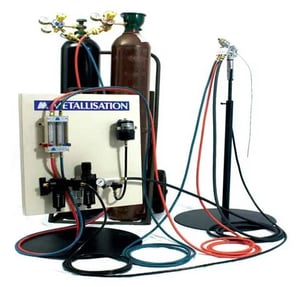
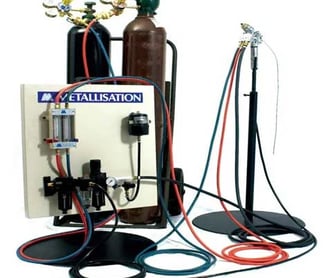
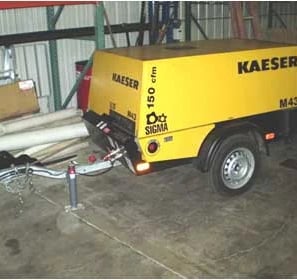
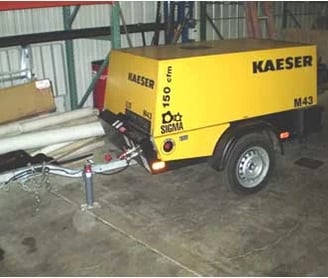
Fired by Oxygen and Acetylene
Thermal ARC Spray
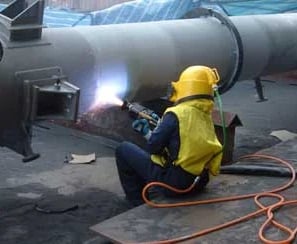
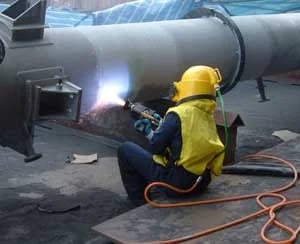
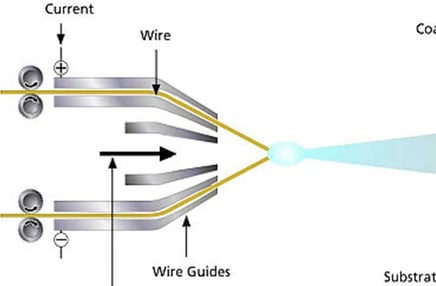
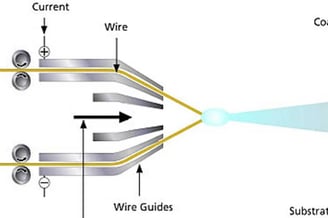

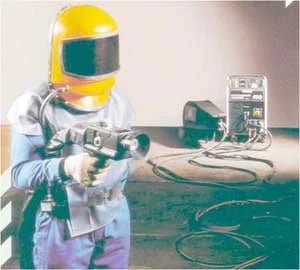
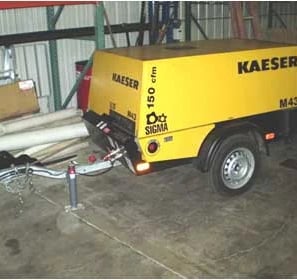
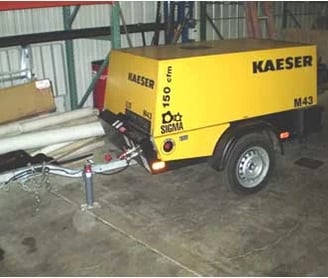
Arc Spray Set-up
3 phase AC, 415 Volt,50 Hz,50 amps
Thermal Spray Coating
Arc Spray
The most suitable for corrosion protection and the preferred method by Oil & Gas Industries.
Excellent adhesive and cohesive strength.
Why TSC is Specified
Require up to 30 years life expectancy in harsh environment.
Currently standard conventional heavy duty coating systems- last only 3 to 5 years.
Consumables
Aluminium
Zinc
Copper
Other Alloys
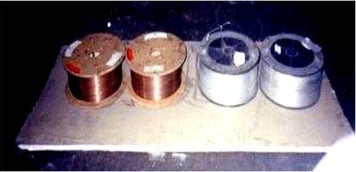
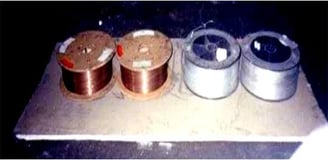
TSC Characteristics
Reduce Corrosion Allowance of Steel
Immediate Solidification submerge/commissioning
No Pot/Shelf Life
Inspection - Almost Instantly
Thermal Spray Coating System
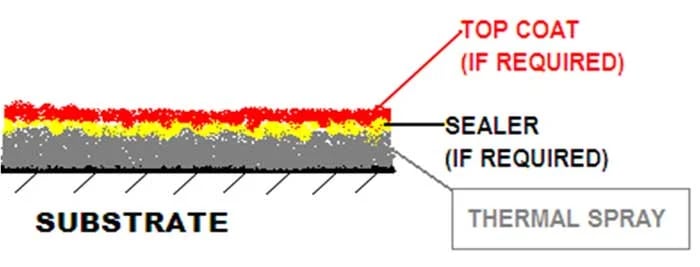
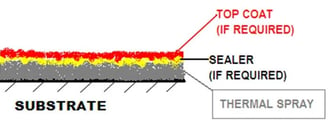
Skilled & Qualified Thermal Spray Applicators
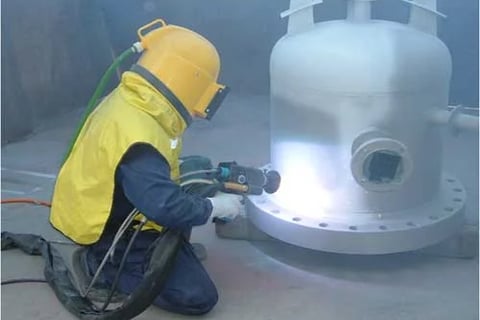

Surface Porosity
Porosity is inevitable in thermal spray coatings
Require sealer to seal the porosity
Sealer comply with service condition
Example: silicone-aluminium, epoxy, polyurethane sealers.
Sealer
Epoxy: to a maximum temperature of 120 °C
Silicone: to a maximum temperature of 450°C
Thickness ≤ 40 microns DFT
Low viscosity
No sealer required immersed or underground
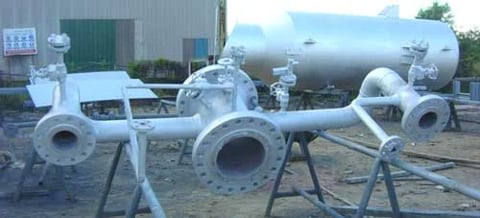
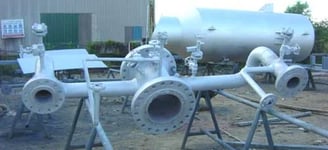
Quality Assurance
ISO 14918 Thermal Sprayer Pre-qualification tests
Dry Film Thickness
Adhesion Strength
Flexibility (Bend Test)
Areas for Thermal Spray Coatings
Corrosion Protection
Splash Zone Areas – no maintenance required
High Temperature up to 600 °C
Cyclic Temperature
Corrosion Under Insulation – CUI
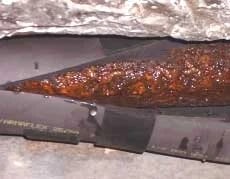
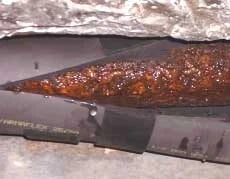